Common Production Processes for Capacitor Manufacturers
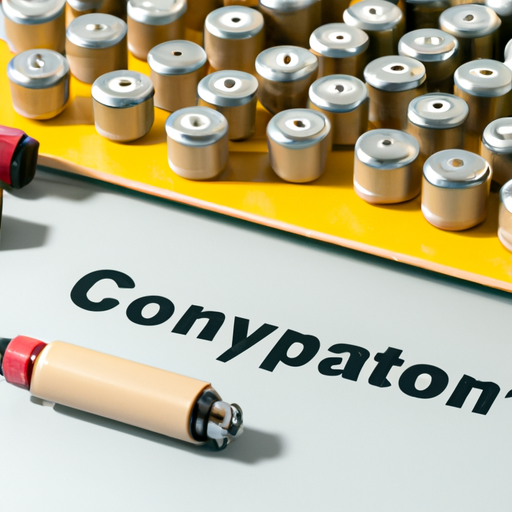
I. Introduction
Capacitors are essential components in electronic devices, serving as energy storage units that can release energy quickly when needed. They play a crucial role in various applications, from filtering signals in audio equipment to stabilizing voltage in power supplies. The capacitor manufacturing industry is a vital segment of the electronics sector, driven by the increasing demand for electronic devices across various industries, including consumer electronics, automotive, telecommunications, and renewable energy.
In this blog post, we will explore the common production processes for capacitor manufacturers, delving into the different types of capacitors, the materials used, the manufacturing stages, quality control measures, challenges faced by manufacturers, and future trends in the industry.
II. Types of Capacitors
Capacitors come in various types, each designed for specific applications and performance characteristics. The most common types include:
A. Ceramic Capacitors
Ceramic capacitors are widely used due to their small size, low cost, and reliability. They are often found in high-frequency applications and are available in various capacitance values.
B. Electrolytic Capacitors
Electrolytic capacitors are polarized components that offer high capacitance values in a compact form. They are commonly used in power supply circuits and audio applications.
C. Film Capacitors
Film capacitors are known for their stability and low loss characteristics. They are often used in applications requiring high precision, such as audio equipment and power electronics.
D. Tantalum Capacitors
Tantalum capacitors are known for their high capacitance-to-volume ratio and reliability. They are often used in military and aerospace applications, as well as in portable electronics.
E. Supercapacitors
Supercapacitors, or ultracapacitors, are designed for high energy storage and rapid charge/discharge cycles. They are increasingly used in applications such as energy harvesting and electric vehicles.
F. Comparison of Different Types and Their Applications
Each type of capacitor has its unique advantages and is suited for specific applications. Understanding these differences is crucial for manufacturers and designers when selecting the appropriate capacitor for a given application.
III. Overview of the Manufacturing Process
The manufacturing process for capacitors generally involves several key stages, including material preparation, component assembly, and testing. Quality control is paramount throughout the production process to ensure that the final products meet industry standards and customer expectations.
IV. Raw Materials
A. Types of Materials Used in Capacitor Production
The production of capacitors requires various raw materials, including:
1. **Dielectric Materials**: These materials, such as ceramic, plastic film, or tantalum oxide, serve as the insulating layer between the capacitor's electrodes.
2. **Conductive Materials**: Metals like aluminum, tantalum, and silver are used for the electrodes and connections.
3. **Packaging Materials**: These materials protect the capacitor and ensure its longevity, often including plastics and metal casings.
B. Sourcing and Quality of Raw Materials
The quality of raw materials directly impacts the performance and reliability of capacitors. Manufacturers must establish strong relationships with suppliers to ensure consistent quality and availability of materials.
V. Production Processes
A. Ceramic Capacitors
1. **Material Preparation**: The process begins with the preparation of ceramic powders, which are mixed with additives to achieve the desired dielectric properties.
2. **Dielectric Layer Formation**: The mixture is then formed into thin layers, often using techniques like tape casting or screen printing.
3. **Electrode Application**: Conductive materials are applied to the dielectric layers to create electrodes.
4. **Sintering Process**: The assembled layers are subjected to high temperatures in a sintering furnace, which densifies the ceramic and forms a solid capacitor structure.
5. **Finishing and Testing**: After cooling, the capacitors undergo finishing processes, including trimming and testing for electrical performance.
B. Electrolytic Capacitors
1. **Anode Foil Preparation**: The process starts with the preparation of aluminum or tantalum foil, which serves as the anode.
2. **Dielectric Formation**: A thin layer of oxide is formed on the anode surface through an electrochemical process, creating the dielectric.
3. **Electrolyte Filling**: The capacitor is filled with an electrolyte solution, which enhances its capacitance.
4. **Sealing and Packaging**: The capacitor is sealed to prevent leakage and packaged for distribution.
C. Film Capacitors
1. **Film Production**: The manufacturing process begins with the production of thin plastic films, which serve as the dielectric.
2. **Metallization**: A thin layer of metal is deposited onto the film to create the electrodes.
3. **Winding and Assembly**: The metallized film is wound into a cylindrical shape and assembled into a capacitor casing.
4. **Testing and Quality Assurance**: The finished capacitors undergo rigorous testing to ensure they meet performance specifications.
D. Tantalum Capacitors
1. **Tantalum Powder Preparation**: Tantalum powder is processed to achieve the desired particle size and purity.
2. **Anode Formation**: The powder is compacted and sintered to form the anode.
3. **Dielectric Formation**: An oxide layer is formed on the anode through an electrochemical process.
4. **Packaging and Testing**: The capacitors are packaged and tested for reliability and performance.
E. Supercapacitors
1. **Electrode Preparation**: The electrodes are made from materials like activated carbon, which provide high surface area for energy storage.
2. **Electrolyte Selection**: A suitable electrolyte is chosen to optimize performance.
3. **Assembly and Testing**: The electrodes and electrolyte are assembled into a cell, which is then tested for performance and reliability.
VI. Quality Control and Testing
A. Importance of Quality Assurance in Capacitor Manufacturing
Quality assurance is critical in capacitor manufacturing, as defects can lead to failures in electronic devices. Manufacturers must implement stringent quality control measures throughout the production process.
B. Common Testing Methods
1. **Electrical Testing**: Capacitors are tested for capacitance, equivalent series resistance (ESR), and leakage current.
2. **Environmental Testing**: Capacitors undergo tests to assess their performance under various environmental conditions, such as temperature and humidity.
3. **Reliability Testing**: Long-term reliability tests are conducted to ensure that capacitors can withstand operational stresses over time.
C. Compliance with Industry Standards
Manufacturers must comply with industry standards, such as ISO and IEC, to ensure that their products meet safety and performance requirements.
VII. Challenges in Capacitor Manufacturing
A. Material Sourcing and Cost Fluctuations
The availability and cost of raw materials can fluctuate, impacting production costs and profitability. Manufacturers must navigate these challenges to maintain competitive pricing.
B. Technological Advancements and Innovation
The rapid pace of technological advancements requires manufacturers to continuously innovate and improve their production processes to meet evolving market demands.
C. Environmental Regulations and Sustainability
Manufacturers face increasing pressure to adopt sustainable practices and comply with environmental regulations, which can impact production methods and costs.
D. Competition in the Global Market
The capacitor manufacturing industry is highly competitive, with numerous players vying for market share. Manufacturers must differentiate their products and maintain high-quality standards to succeed.
VIII. Future Trends in Capacitor Manufacturing
A. Advancements in Materials and Technology
Research and development efforts are focused on discovering new materials and technologies that can enhance capacitor performance and reduce costs.
B. Increasing Demand for Miniaturization and Efficiency
As electronic devices become smaller and more efficient, the demand for compact and high-performance capacitors will continue to grow.
C. The Role of Automation and Industry 4.0
Automation and smart manufacturing technologies are transforming the capacitor production landscape, improving efficiency and reducing labor costs.
D. Sustainability Initiatives in Capacitor Production
Manufacturers are increasingly adopting sustainable practices, such as recycling materials and reducing waste, to minimize their environmental impact.
IX. Conclusion
Capacitors are integral components in modern electronic devices, and their manufacturing processes are complex and multifaceted. From the selection of raw materials to the final testing of finished products, each stage of production is critical to ensuring quality and reliability. As the capacitor manufacturing industry continues to evolve, manufacturers must adapt to new challenges and embrace innovations that will shape the future of capacitor production. The ongoing advancements in materials, technology, and sustainability initiatives will play a significant role in meeting the growing demand for capacitors in an increasingly electronic world.
Common Production Processes for Capacitor Manufacturers
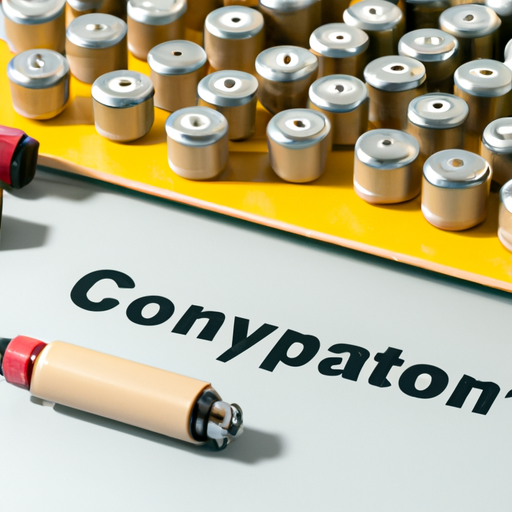
I. Introduction
Capacitors are essential components in electronic devices, serving as energy storage units that can release energy quickly when needed. They play a crucial role in various applications, from filtering signals in audio equipment to stabilizing voltage in power supplies. The capacitor manufacturing industry is a vital segment of the electronics sector, driven by the increasing demand for electronic devices across various industries, including consumer electronics, automotive, telecommunications, and renewable energy.
In this blog post, we will explore the common production processes for capacitor manufacturers, delving into the different types of capacitors, the materials used, the manufacturing stages, quality control measures, challenges faced by manufacturers, and future trends in the industry.
II. Types of Capacitors
Capacitors come in various types, each designed for specific applications and performance characteristics. The most common types include:
A. Ceramic Capacitors
Ceramic capacitors are widely used due to their small size, low cost, and reliability. They are often found in high-frequency applications and are available in various capacitance values.
B. Electrolytic Capacitors
Electrolytic capacitors are polarized components that offer high capacitance values in a compact form. They are commonly used in power supply circuits and audio applications.
C. Film Capacitors
Film capacitors are known for their stability and low loss characteristics. They are often used in applications requiring high precision, such as audio equipment and power electronics.
D. Tantalum Capacitors
Tantalum capacitors are known for their high capacitance-to-volume ratio and reliability. They are often used in military and aerospace applications, as well as in portable electronics.
E. Supercapacitors
Supercapacitors, or ultracapacitors, are designed for high energy storage and rapid charge/discharge cycles. They are increasingly used in applications such as energy harvesting and electric vehicles.
F. Comparison of Different Types and Their Applications
Each type of capacitor has its unique advantages and is suited for specific applications. Understanding these differences is crucial for manufacturers and designers when selecting the appropriate capacitor for a given application.
III. Overview of the Manufacturing Process
The manufacturing process for capacitors generally involves several key stages, including material preparation, component assembly, and testing. Quality control is paramount throughout the production process to ensure that the final products meet industry standards and customer expectations.
IV. Raw Materials
A. Types of Materials Used in Capacitor Production
The production of capacitors requires various raw materials, including:
1. **Dielectric Materials**: These materials, such as ceramic, plastic film, or tantalum oxide, serve as the insulating layer between the capacitor's electrodes.
2. **Conductive Materials**: Metals like aluminum, tantalum, and silver are used for the electrodes and connections.
3. **Packaging Materials**: These materials protect the capacitor and ensure its longevity, often including plastics and metal casings.
B. Sourcing and Quality of Raw Materials
The quality of raw materials directly impacts the performance and reliability of capacitors. Manufacturers must establish strong relationships with suppliers to ensure consistent quality and availability of materials.
V. Production Processes
A. Ceramic Capacitors
1. **Material Preparation**: The process begins with the preparation of ceramic powders, which are mixed with additives to achieve the desired dielectric properties.
2. **Dielectric Layer Formation**: The mixture is then formed into thin layers, often using techniques like tape casting or screen printing.
3. **Electrode Application**: Conductive materials are applied to the dielectric layers to create electrodes.
4. **Sintering Process**: The assembled layers are subjected to high temperatures in a sintering furnace, which densifies the ceramic and forms a solid capacitor structure.
5. **Finishing and Testing**: After cooling, the capacitors undergo finishing processes, including trimming and testing for electrical performance.
B. Electrolytic Capacitors
1. **Anode Foil Preparation**: The process starts with the preparation of aluminum or tantalum foil, which serves as the anode.
2. **Dielectric Formation**: A thin layer of oxide is formed on the anode surface through an electrochemical process, creating the dielectric.
3. **Electrolyte Filling**: The capacitor is filled with an electrolyte solution, which enhances its capacitance.
4. **Sealing and Packaging**: The capacitor is sealed to prevent leakage and packaged for distribution.
C. Film Capacitors
1. **Film Production**: The manufacturing process begins with the production of thin plastic films, which serve as the dielectric.
2. **Metallization**: A thin layer of metal is deposited onto the film to create the electrodes.
3. **Winding and Assembly**: The metallized film is wound into a cylindrical shape and assembled into a capacitor casing.
4. **Testing and Quality Assurance**: The finished capacitors undergo rigorous testing to ensure they meet performance specifications.
D. Tantalum Capacitors
1. **Tantalum Powder Preparation**: Tantalum powder is processed to achieve the desired particle size and purity.
2. **Anode Formation**: The powder is compacted and sintered to form the anode.
3. **Dielectric Formation**: An oxide layer is formed on the anode through an electrochemical process.
4. **Packaging and Testing**: The capacitors are packaged and tested for reliability and performance.
E. Supercapacitors
1. **Electrode Preparation**: The electrodes are made from materials like activated carbon, which provide high surface area for energy storage.
2. **Electrolyte Selection**: A suitable electrolyte is chosen to optimize performance.
3. **Assembly and Testing**: The electrodes and electrolyte are assembled into a cell, which is then tested for performance and reliability.
VI. Quality Control and Testing
A. Importance of Quality Assurance in Capacitor Manufacturing
Quality assurance is critical in capacitor manufacturing, as defects can lead to failures in electronic devices. Manufacturers must implement stringent quality control measures throughout the production process.
B. Common Testing Methods
1. **Electrical Testing**: Capacitors are tested for capacitance, equivalent series resistance (ESR), and leakage current.
2. **Environmental Testing**: Capacitors undergo tests to assess their performance under various environmental conditions, such as temperature and humidity.
3. **Reliability Testing**: Long-term reliability tests are conducted to ensure that capacitors can withstand operational stresses over time.
C. Compliance with Industry Standards
Manufacturers must comply with industry standards, such as ISO and IEC, to ensure that their products meet safety and performance requirements.
VII. Challenges in Capacitor Manufacturing
A. Material Sourcing and Cost Fluctuations
The availability and cost of raw materials can fluctuate, impacting production costs and profitability. Manufacturers must navigate these challenges to maintain competitive pricing.
B. Technological Advancements and Innovation
The rapid pace of technological advancements requires manufacturers to continuously innovate and improve their production processes to meet evolving market demands.
C. Environmental Regulations and Sustainability
Manufacturers face increasing pressure to adopt sustainable practices and comply with environmental regulations, which can impact production methods and costs.
D. Competition in the Global Market
The capacitor manufacturing industry is highly competitive, with numerous players vying for market share. Manufacturers must differentiate their products and maintain high-quality standards to succeed.
VIII. Future Trends in Capacitor Manufacturing
A. Advancements in Materials and Technology
Research and development efforts are focused on discovering new materials and technologies that can enhance capacitor performance and reduce costs.
B. Increasing Demand for Miniaturization and Efficiency
As electronic devices become smaller and more efficient, the demand for compact and high-performance capacitors will continue to grow.
C. The Role of Automation and Industry 4.0
Automation and smart manufacturing technologies are transforming the capacitor production landscape, improving efficiency and reducing labor costs.
D. Sustainability Initiatives in Capacitor Production
Manufacturers are increasingly adopting sustainable practices, such as recycling materials and reducing waste, to minimize their environmental impact.
IX. Conclusion
Capacitors are integral components in modern electronic devices, and their manufacturing processes are complex and multifaceted. From the selection of raw materials to the final testing of finished products, each stage of production is critical to ensuring quality and reliability. As the capacitor manufacturing industry continues to evolve, manufacturers must adapt to new challenges and embrace innovations that will shape the future of capacitor production. The ongoing advancements in materials, technology, and sustainability initiatives will play a significant role in meeting the growing demand for capacitors in an increasingly electronic world.