What are the Product Standards for Resistor Classification?
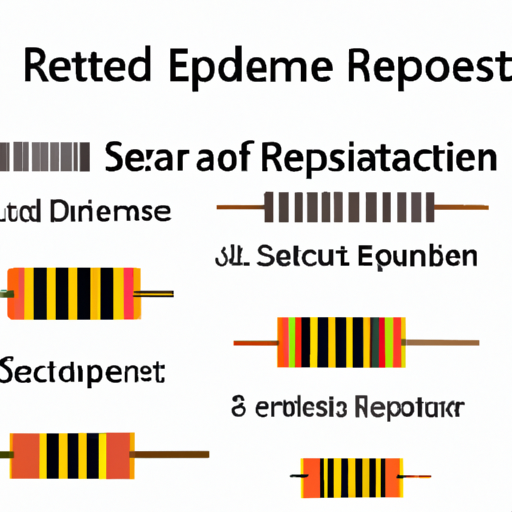
I. Introduction
Resistors are fundamental components in electronic circuits, serving the critical function of controlling current flow. They are essential for managing voltage levels, dividing voltages, and protecting sensitive components from excessive current. Given their ubiquitous presence in electronic devices, the classification of resistors according to specific standards is vital for ensuring their reliability and performance. Product standards provide a framework for evaluating and categorizing resistors, ensuring that they meet the necessary specifications for various applications. This blog post will explore the product standards for resistor classification, delving into the types of resistors, key parameters for classification, and the relevant international and national standards.
II. Understanding Resistor Classification
A. Types of Resistors
Resistors can be broadly classified into three categories:
1. **Fixed Resistors**: These resistors have a constant resistance value and are the most commonly used type. They are available in various materials, including carbon, metal film, and wire-wound.
2. **Variable Resistors**: Also known as potentiometers or rheostats, these resistors allow for adjustable resistance values. They are often used in applications where tuning or calibration is necessary, such as volume controls in audio equipment.
3. **Specialty Resistors**: This category includes a variety of resistors designed for specific applications, such as thermistors (temperature-sensitive resistors), photoresistors (light-sensitive resistors), and current sensing resistors.
B. Key Parameters for Classification
When classifying resistors, several key parameters are considered:
1. **Resistance Value**: Measured in ohms (Ω), this value indicates the resistor's opposition to current flow.
2. **Tolerance**: This parameter defines the allowable deviation from the nominal resistance value, expressed as a percentage. For example, a resistor with a tolerance of ±5% can have a resistance value that varies by 5% above or below its stated value.
3. **Power Rating**: Measured in watts (W), this indicates the maximum power the resistor can dissipate without overheating. Exceeding this rating can lead to failure.
4. **Temperature Coefficient**: This parameter indicates how much the resistance value changes with temperature, typically expressed in parts per million per degree Celsius (ppm/°C).
5. **Voltage Rating**: This specifies the maximum voltage that can be applied across the resistor without risk of breakdown or failure.
III. International Standards for Resistor Classification
A. Overview of International Standards Organizations
Several international organizations establish standards for electronic components, including resistors:
1. **International Electrotechnical Commission (IEC)**: The IEC develops international standards for electrical and electronic technologies, including resistors.
2. **Institute of Electrical and Electronics Engineers (IEEE)**: IEEE standards cover a wide range of electrical and electronic components, providing guidelines for performance and safety.
3. **American National Standards Institute (ANSI)**: ANSI oversees the development of voluntary consensus standards for products, services, processes, and systems in the United States.
B. Key Standards Relevant to Resistors
Several key standards govern resistor classification:
1. **IEC 60115 Series**: This series of standards specifies the general requirements, testing methods, and performance characteristics for fixed resistors.
2. **IEEE 18**: This standard outlines the specifications for resistors used in electrical power systems, focusing on performance and reliability.
3. **ANSI/IEEE C57.12.01**: This standard provides guidelines for the testing and performance of resistors used in power transformers and other electrical equipment.
IV. National Standards for Resistor Classification
A. Overview of National Standards Organizations
In addition to international standards, various national organizations establish standards for resistors:
1. **American Society for Testing and Materials (ASTM)**: ASTM develops technical standards for materials, products, systems, and services, including resistors.
2. **Underwriters Laboratories (UL)**: UL is a safety certification organization that tests and certifies products for safety and performance, including electronic components.
3. **Japanese Industrial Standards (JIS)**: JIS establishes standards for industrial products in Japan, including resistors.
B. Key National Standards Relevant to Resistors
Some important national standards include:
1. **ASTM D257**: This standard outlines the test methods for measuring the resistivity of insulating materials, which is relevant for resistor performance.
2. **UL 1412**: This standard covers the safety requirements for resistors used in electrical equipment, ensuring they meet safety and performance criteria.
3. **JIS C 5201**: This standard specifies the general requirements for fixed resistors, including testing methods and performance characteristics.
V. Key Parameters in Resistor Standards
A. Resistance Value
1. **Measurement Units and Ranges**: Resistance is measured in ohms, with standard values typically falling within the E12 and E24 series. These series provide a set of preferred numbers for resistors, ensuring consistency in manufacturing and selection.
2. **Standard Values and E12/E24 Series**: The E12 series includes values like 10, 12, 15, 18, and so on, while the E24 series offers a more precise range, including values like 10.0, 10.2, 10.5, etc. These series help designers select appropriate resistor values for their circuits.
B. Tolerance
1. **Definition and Importance**: Tolerance indicates how much a resistor's actual resistance can deviate from its nominal value. It is crucial for ensuring circuit performance, as components with tighter tolerances provide more predictable behavior.
2. **Standard Tolerance Classes**: Common tolerance classes include ±1%, ±5%, and ±10%, with precision resistors often having tolerances as low as ±0.1%.
C. Power Rating
1. **Definition and Significance**: The power rating indicates the maximum power a resistor can handle without overheating. It is essential for preventing failure in circuits where high currents are present.
2. **Standard Power Ratings and Testing Methods**: Power ratings typically range from 1/8 W to several hundred watts, depending on the resistor type. Testing methods include applying a known voltage and measuring the resulting current to calculate power dissipation.
D. Temperature Coefficient
1. **Explanation of Temperature Coefficient**: The temperature coefficient indicates how much a resistor's resistance changes with temperature. A lower temperature coefficient is desirable for applications requiring stable performance across varying temperatures.
2. **Standard Classifications (ppm/°C)**: Common classifications include ±50 ppm/°C, ±100 ppm/°C, and ±200 ppm/°C, with lower values indicating better temperature stability.
E. Voltage Rating
1. **Importance of Voltage Rating**: The voltage rating is critical for ensuring that a resistor can handle the voltage applied without breaking down. Exceeding this rating can lead to catastrophic failure.
2. **Standard Voltage Ratings and Testing Methods**: Voltage ratings vary widely, with standard values often ranging from a few volts to several kilovolts. Testing methods include applying a specified voltage and monitoring for breakdown or failure.
VI. Testing and Quality Assurance
A. Importance of Testing in Resistor Classification
Testing is essential for verifying that resistors meet the specified standards and performance criteria. It ensures that components are reliable and safe for use in electronic circuits.
B. Common Testing Methods
1. **Resistance Measurement**: This involves using precision instruments to measure the actual resistance value and compare it to the nominal value.
2. **Power Rating Tests**: These tests assess a resistor's ability to handle specified power levels without overheating or failing.
3. **Environmental Testing**: Resistors may undergo environmental tests to evaluate their performance under various conditions, such as temperature extremes and humidity.
C. Quality Assurance Processes
1. **Certification and Compliance**: Many manufacturers seek certification from recognized standards organizations to demonstrate compliance with relevant standards.
2. **Role of Third-Party Testing Organizations**: Independent testing organizations play a crucial role in verifying that resistors meet the required standards, providing an additional layer of assurance for manufacturers and consumers.
VII. Conclusion
In summary, product standards for resistor classification are vital for ensuring the reliability and performance of these essential electronic components. By adhering to international and national standards, manufacturers can produce resistors that meet the necessary specifications for various applications. As technology continues to evolve, the standards governing resistors will likely adapt to address new challenges and innovations in the field. Ultimately, these standards play a crucial role in ensuring that electronic devices function as intended, providing safety and reliability for consumers and industries alike.
VIII. References
1. IEC 60115 Series - International Electrotechnical Commission
2. IEEE 18 - Institute of Electrical and Electronics Engineers
3. ANSI/IEEE C57.12.01 - American National Standards Institute
4. ASTM D257 - American Society for Testing and Materials
5. UL 1412 - Underwriters Laboratories
6. JIS C 5201 - Japanese Industrial Standards
For further reading on resistor standards and testing methods, consider exploring academic publications and industry resources that delve deeper into the specifications and applications of resistors in electronic circuits.
What are the Product Standards for Resistor Classification?
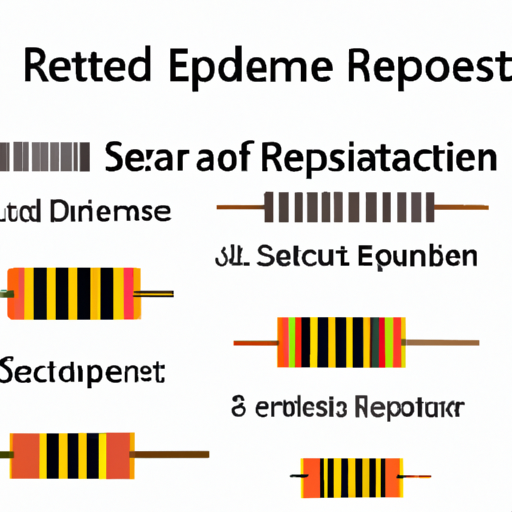
I. Introduction
Resistors are fundamental components in electronic circuits, serving the critical function of controlling current flow. They are essential for managing voltage levels, dividing voltages, and protecting sensitive components from excessive current. Given their ubiquitous presence in electronic devices, the classification of resistors according to specific standards is vital for ensuring their reliability and performance. Product standards provide a framework for evaluating and categorizing resistors, ensuring that they meet the necessary specifications for various applications. This blog post will explore the product standards for resistor classification, delving into the types of resistors, key parameters for classification, and the relevant international and national standards.
II. Understanding Resistor Classification
A. Types of Resistors
Resistors can be broadly classified into three categories:
1. **Fixed Resistors**: These resistors have a constant resistance value and are the most commonly used type. They are available in various materials, including carbon, metal film, and wire-wound.
2. **Variable Resistors**: Also known as potentiometers or rheostats, these resistors allow for adjustable resistance values. They are often used in applications where tuning or calibration is necessary, such as volume controls in audio equipment.
3. **Specialty Resistors**: This category includes a variety of resistors designed for specific applications, such as thermistors (temperature-sensitive resistors), photoresistors (light-sensitive resistors), and current sensing resistors.
B. Key Parameters for Classification
When classifying resistors, several key parameters are considered:
1. **Resistance Value**: Measured in ohms (Ω), this value indicates the resistor's opposition to current flow.
2. **Tolerance**: This parameter defines the allowable deviation from the nominal resistance value, expressed as a percentage. For example, a resistor with a tolerance of ±5% can have a resistance value that varies by 5% above or below its stated value.
3. **Power Rating**: Measured in watts (W), this indicates the maximum power the resistor can dissipate without overheating. Exceeding this rating can lead to failure.
4. **Temperature Coefficient**: This parameter indicates how much the resistance value changes with temperature, typically expressed in parts per million per degree Celsius (ppm/°C).
5. **Voltage Rating**: This specifies the maximum voltage that can be applied across the resistor without risk of breakdown or failure.
III. International Standards for Resistor Classification
A. Overview of International Standards Organizations
Several international organizations establish standards for electronic components, including resistors:
1. **International Electrotechnical Commission (IEC)**: The IEC develops international standards for electrical and electronic technologies, including resistors.
2. **Institute of Electrical and Electronics Engineers (IEEE)**: IEEE standards cover a wide range of electrical and electronic components, providing guidelines for performance and safety.
3. **American National Standards Institute (ANSI)**: ANSI oversees the development of voluntary consensus standards for products, services, processes, and systems in the United States.
B. Key Standards Relevant to Resistors
Several key standards govern resistor classification:
1. **IEC 60115 Series**: This series of standards specifies the general requirements, testing methods, and performance characteristics for fixed resistors.
2. **IEEE 18**: This standard outlines the specifications for resistors used in electrical power systems, focusing on performance and reliability.
3. **ANSI/IEEE C57.12.01**: This standard provides guidelines for the testing and performance of resistors used in power transformers and other electrical equipment.
IV. National Standards for Resistor Classification
A. Overview of National Standards Organizations
In addition to international standards, various national organizations establish standards for resistors:
1. **American Society for Testing and Materials (ASTM)**: ASTM develops technical standards for materials, products, systems, and services, including resistors.
2. **Underwriters Laboratories (UL)**: UL is a safety certification organization that tests and certifies products for safety and performance, including electronic components.
3. **Japanese Industrial Standards (JIS)**: JIS establishes standards for industrial products in Japan, including resistors.
B. Key National Standards Relevant to Resistors
Some important national standards include:
1. **ASTM D257**: This standard outlines the test methods for measuring the resistivity of insulating materials, which is relevant for resistor performance.
2. **UL 1412**: This standard covers the safety requirements for resistors used in electrical equipment, ensuring they meet safety and performance criteria.
3. **JIS C 5201**: This standard specifies the general requirements for fixed resistors, including testing methods and performance characteristics.
V. Key Parameters in Resistor Standards
A. Resistance Value
1. **Measurement Units and Ranges**: Resistance is measured in ohms, with standard values typically falling within the E12 and E24 series. These series provide a set of preferred numbers for resistors, ensuring consistency in manufacturing and selection.
2. **Standard Values and E12/E24 Series**: The E12 series includes values like 10, 12, 15, 18, and so on, while the E24 series offers a more precise range, including values like 10.0, 10.2, 10.5, etc. These series help designers select appropriate resistor values for their circuits.
B. Tolerance
1. **Definition and Importance**: Tolerance indicates how much a resistor's actual resistance can deviate from its nominal value. It is crucial for ensuring circuit performance, as components with tighter tolerances provide more predictable behavior.
2. **Standard Tolerance Classes**: Common tolerance classes include ±1%, ±5%, and ±10%, with precision resistors often having tolerances as low as ±0.1%.
C. Power Rating
1. **Definition and Significance**: The power rating indicates the maximum power a resistor can handle without overheating. It is essential for preventing failure in circuits where high currents are present.
2. **Standard Power Ratings and Testing Methods**: Power ratings typically range from 1/8 W to several hundred watts, depending on the resistor type. Testing methods include applying a known voltage and measuring the resulting current to calculate power dissipation.
D. Temperature Coefficient
1. **Explanation of Temperature Coefficient**: The temperature coefficient indicates how much a resistor's resistance changes with temperature. A lower temperature coefficient is desirable for applications requiring stable performance across varying temperatures.
2. **Standard Classifications (ppm/°C)**: Common classifications include ±50 ppm/°C, ±100 ppm/°C, and ±200 ppm/°C, with lower values indicating better temperature stability.
E. Voltage Rating
1. **Importance of Voltage Rating**: The voltage rating is critical for ensuring that a resistor can handle the voltage applied without breaking down. Exceeding this rating can lead to catastrophic failure.
2. **Standard Voltage Ratings and Testing Methods**: Voltage ratings vary widely, with standard values often ranging from a few volts to several kilovolts. Testing methods include applying a specified voltage and monitoring for breakdown or failure.
VI. Testing and Quality Assurance
A. Importance of Testing in Resistor Classification
Testing is essential for verifying that resistors meet the specified standards and performance criteria. It ensures that components are reliable and safe for use in electronic circuits.
B. Common Testing Methods
1. **Resistance Measurement**: This involves using precision instruments to measure the actual resistance value and compare it to the nominal value.
2. **Power Rating Tests**: These tests assess a resistor's ability to handle specified power levels without overheating or failing.
3. **Environmental Testing**: Resistors may undergo environmental tests to evaluate their performance under various conditions, such as temperature extremes and humidity.
C. Quality Assurance Processes
1. **Certification and Compliance**: Many manufacturers seek certification from recognized standards organizations to demonstrate compliance with relevant standards.
2. **Role of Third-Party Testing Organizations**: Independent testing organizations play a crucial role in verifying that resistors meet the required standards, providing an additional layer of assurance for manufacturers and consumers.
VII. Conclusion
In summary, product standards for resistor classification are vital for ensuring the reliability and performance of these essential electronic components. By adhering to international and national standards, manufacturers can produce resistors that meet the necessary specifications for various applications. As technology continues to evolve, the standards governing resistors will likely adapt to address new challenges and innovations in the field. Ultimately, these standards play a crucial role in ensuring that electronic devices function as intended, providing safety and reliability for consumers and industries alike.
VIII. References
1. IEC 60115 Series - International Electrotechnical Commission
2. IEEE 18 - Institute of Electrical and Electronics Engineers
3. ANSI/IEEE C57.12.01 - American National Standards Institute
4. ASTM D257 - American Society for Testing and Materials
5. UL 1412 - Underwriters Laboratories
6. JIS C 5201 - Japanese Industrial Standards
For further reading on resistor standards and testing methods, consider exploring academic publications and industry resources that delve deeper into the specifications and applications of resistors in electronic circuits.